Proces formowania i produkcji tworzyw sztucznych: Top 7 Techniques
Przedmioty z tworzyw sztucznych można oczywiście znaleźć wszędzie w naszym codziennym życiu, ale wiele osób nie wie, że istnieją różne sposoby ich formowania do użytku komercyjnego lub przemysłowego. Oto siedem najbardziej powszechnych metod i co musisz wiedzieć, aby zdecydować, która z nich jest najlepsza dla twojego następnego projektu.
Formowanie wtryskowe tworzyw sztucznych
Formowanie wtryskowe tworzyw sztucznych stanowi około 80% trwałych przedmiotów z tworzyw sztucznych, które spotykamy na co dzień. Formowanie wtryskowe wykorzystuje formę lub matrycę wykonaną z aluminium lub stali. Forma składa się z rdzenia strony i strony wnęki, która jest umieszczona w plastikowej wtryskarce. Ta maszyna podgrzewa surowe granulki żywicy z tworzywa sztucznego, aż są stopione, wstrzykuje je do pustej wnęki formy pod dużym ciśnieniem, a następnie otwiera się, aby wyrzucić gotową część.
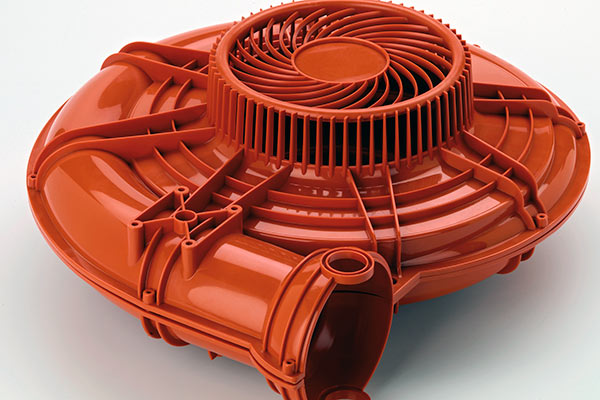
Formowanie dmuchawy wykonane za pomocą maszyny formującej o dużej pojemności z Semco Plastic Co.
Zaletą PIM jest to, że miliony identycznych części mogą być wykonane szybko, z doskonałym wykończeniem powierzchni i przy niskich kosztach. Formy jednak mogą być drogie i skomplikowane, w zależności od geometrii części. Staranny projekt inżynieryjny formy jest wymagany, aby zapobiec wadom i zoptymalizować jakość części i szybkość przetwarzania.
Formowanie rotacyjne (Roto)
Formowanie rotacyjne również wykorzystuje rdzeń i narzędzie do formowania wnęk, ale proces produkcyjny jest zupełnie inny.
Plastikowy proszek jest wlewany do wnęki formy, a forma jest umieszczana w piecu. Podczas ogrzewania, forma jest powoli obracany na dwóch osiach. Grawitacja jest wykorzystywana do przyklejenia tworzywa sztucznego do ścianek narzędzia i uzyskania odpowiedniej grubości.
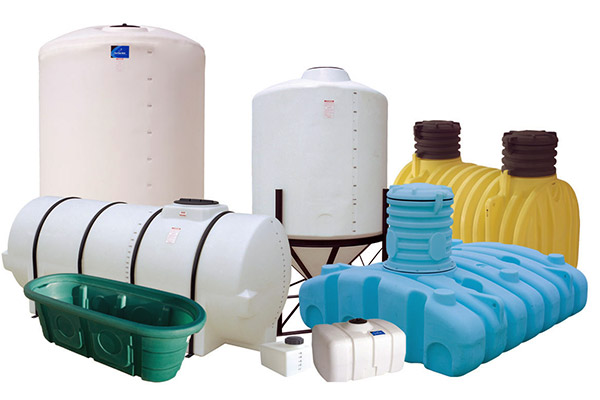
Formowanie rotacyjne jest najlepsze dla dużych pojemników o grubych ściankach.
Następnie forma jest wyjmowana z pieca i powoli chłodzona, aby zapobiec odkształceniom. Pełne chłodzenie może trwać kilka minut, po czym narzędzie jest otwierane, a część usuwana do następnego cyklu.
Formowanie rotacyjne jest idealne do wykonywania dużych, pustych lub wklęsłych kształtów, często do użytku zewnętrznego, takich jak kajaki i wanny. Gotowe części są wolne od naprężeń i nie mają szwów, więc są mocne, a narzędzia są stosunkowo proste i niedrogie do wykonania.Minusem jest to, że narzędzia nie trwają dłużej niż kilka tysięcy cykli, zanim będą musiały być wymienione, a jakość wykończenia części jest średnia w najlepszym przypadku, więc nie nadaje się do formowania precyzyjnego.
Extrusion Blow Molding
Jest to najbardziej powszechny sposób wytwarzania cienkościennych, niedrogich pojemników, takich jak jednorazowe kubki do picia lub butelki. Jest szybki, a narzędzia są łatwe do wykonania, ale części nie mogą być bardzo złożone lub wykonane z wysoką precyzją.
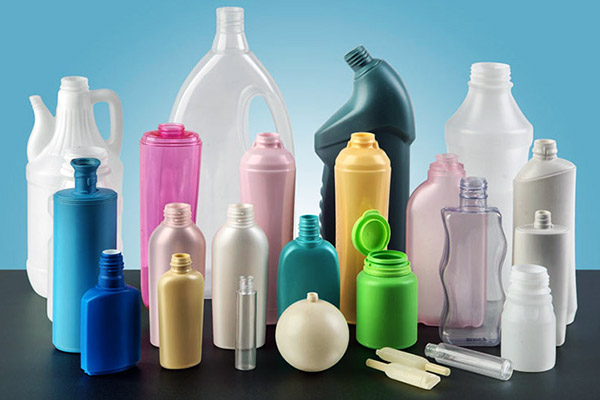
Formowanie wytłaczarkowe jest stosowane do butelek z tworzyw sztucznych.
Roztopione tworzywo sztuczne w postaci dużej kropli, zwanej parisonem, jest umieszczane w dwuczęściowej formie typu clamshell. Po zamknięciu formy, parison jest nadmuchiwany jak balon, aż wypełni pustą przestrzeń. Ponieważ ścianki formy są chłodzone wodą, tworzywo sztuczne szybko krzepnie i butelka może zostać wyrzucona.
Formowanie wtryskowe z rozdmuchem
Podczas formowania wtryskowego z rozdmuchem ciśnienie gazu jest wykorzystywane do wtłaczania roztopionej żywicy do wnęki formy. Proces ten jest łatwo kontrolowany i powtarzalny, i jest powszechnie stosowany do produkcji przezroczystych plastikowych butelek do napojów. Zapewnia on doskonałą jakość powierzchni, ale nie jest idealny do cienkich ścianek.
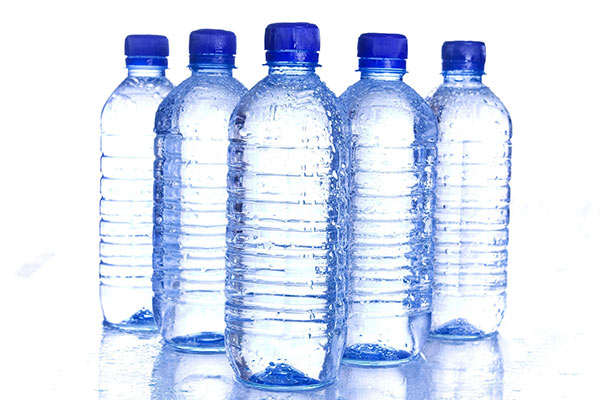
Butelki na wodę PET
PET (politereftalan etylenu) lub PEEK (polieter-eteroketon) to typowe wybory żywicy do butelek na napoje, ze względu na ich przejrzystość i trwałość, a także dlatego, że są oceniane jako bezpieczne dla materiałów eksploatacyjnych. Są one również łatwo poddawane recyklingowi.
Reaction Injection Molding (RIM)
RIM jest najczęściej stosowany w przemyśle motoryzacyjnym, ponieważ produkuje lekkie części, które mają sztywną skórę. Skóra ta jest łatwo malowana w celu wykonania paneli nadwozia, desek rozdzielczych i innych części samochodowych. Jednakże, termoformowanie tworzyw sztucznych nie będzie działać w tym procesie. Zamiast tego proces ten wymaga termoutwardzalnych tworzyw sztucznych.
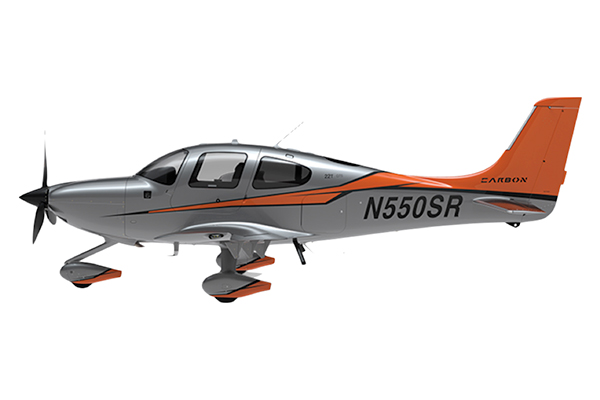
Formowanie rotacyjne zostało użyte do wykonania tych lekkich drzwi samolotu. Dzięki uprzejmości RIM Mfg. LLC.
Tworzywa termoutwardzalne ulegają nieodwracalnej reakcji chemicznej wewnątrz formy. Zwykle powoduje to ich rozszerzanie się jak pianka, wypełniając wnękę formy. Kiedy reakcja chemiczna jest zakończona, tworzywo sztuczne przybiera swoją ostateczną formę.
Koszty oprzyrządowania dla prototypów są stosunkowo niskie, podczas gdy oprzyrządowanie produkcyjne jest umiarkowanie drogie. Główny koszt jest związany z materiałem, pamiętając, że część wynikowa musi być zawsze wykończona, zwykle żelkotem na bazie uretanu lub przez malowanie, więc proces jest bardziej pracochłonny, co zwiększa cenę elementu.
Odlewanie próżniowe
Odlewanie próżniowe jest doskonałym wyborem do wykonania niewielkiej liczby wysokiej jakości szybkich prototypów bez dużych inwestycji w narzędzia lub materiał.
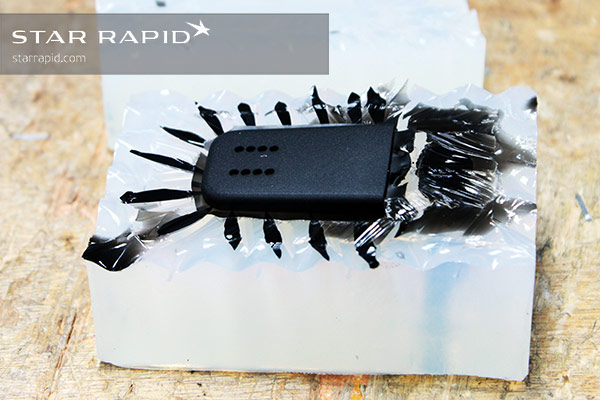
Poliuretanowe odlewanie próżniowe zostało użyte do wykonania tej obudowy w firmie Star Rapid.
Matryca dowolnej sztywnej bryły (często jest to wydrukowany w 3D model wzorcowy) jest umieszczana w szczelnym pudełku, które następnie jest wypełniane elastycznym uretanem lub silikonem. Kiedy matryca jest usuwana, wewnątrz formy powstaje wgłębienie, które może być teraz wypełnione żywicą plastikową, aby utworzyć kopię oryginału. Ciśnienie próżniowe jest używany do wyciągania powietrza z formy tak, że wypełnia całkowicie bez pęcherzyków powietrza.
W tym procesie, jakość wykończenia powierzchni i szczegóły są doskonałe i wylewne żywice mogą imitować wiele klas inżynierii tworzyw sztucznych. Ale formy nie są trwałe i ulegną degradacji po 20 lub więcej kopiach.
Thermoforming
Jest to rodzaj formowania próżniowego, gdzie cienki lub gruby arkusz plastiku jest umieszczany nad matrycą, podgrzewany do temperatury, która pozwala materiałowi stać się giętkim, następnie jest rozciągany nad powierzchnią matrycy, podczas gdy ciśnienie próżniowe ściąga arkusz w dół i do jego ostatecznego kształtu.
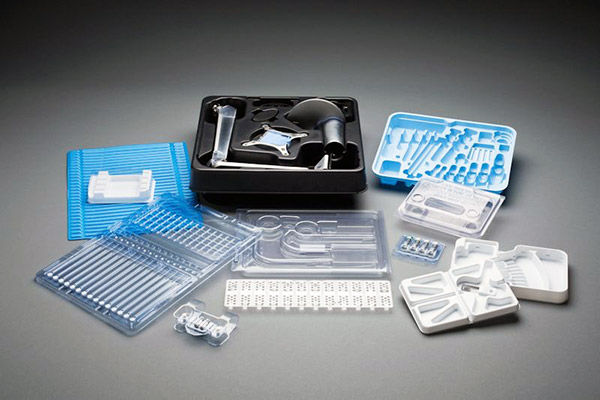
Termoformowanie jest przydatne w przypadku opakowań typu clamshell
Proces ten może być również wykonywany przy użyciu prostych matryc i bardzo podstawowego sprzętu. Jest on często stosowany do próbek i prototypów cienkościennych, pustych w środku części. W przemyśle używa się go do produkcji plastikowych kubków, pokrywek, pudełek i plastikowych opakowań typu clamshell, jak również do produkcji części karoserii samochodowych z grubszych materiałów. Tylko tworzywa termoformowalne są odpowiednie do tego procesu.
Formowanie tłoczne
Produkt jest wstępnie podgrzewany i umieszczany wewnątrz otwartej wnęki matrycy. Zaślepka lub korek jest używany do zamknięcia matrycy i zastosowania ciepła i ciśnienia, powodując utwardzanie tworzywa sztucznego. Proces ten jest doskonały dla gumowych przełączników klawiaturowych, uszczelek, O-ringów i innych miękkich, giętkich części cienkościennych.
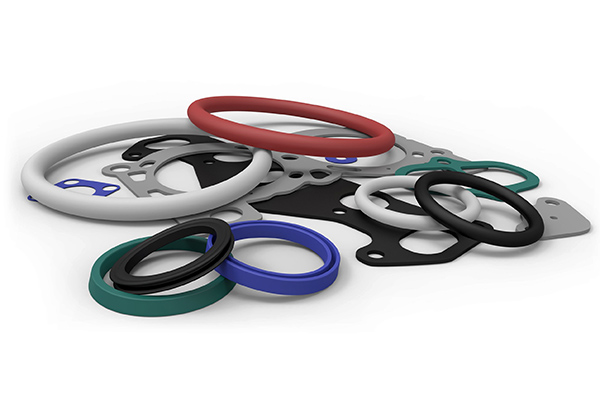
O-ringi z gumy silikonowej wykonane metodą formowania tłocznego
Jest to metoda stosunkowo niedroga i marnuje niewiele materiału, chociaż kontrolowanie konsystencji gotowego elementu może być trudne i należy poświęcić wiele uwagi przygotowaniu wstępnego projektu formy.
Podsumowanie
Star Rapid oferuje szereg rozwiązań, aby pomóc Ci uzyskać dokładnie takie części z tworzyw sztucznych lub gumy, jakich potrzebujesz do swojego projektu. Skontaktuj się z nami już dziś, aby uzyskać więcej informacji i bezpłatną wycenę.